Heidelberger Druckmaschinen AG
(Druck-)Frischer Wind in der Logistik von Heidelberg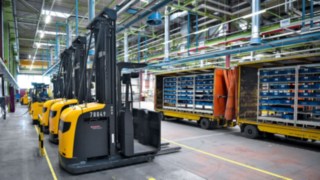
In Zeiten immer individuellerer Kundenwünsche muss sich auch die Intralogistik sukzessive den veränderten Produktionsbedingungen anpassen. Wie das bei einem global agierenden Industrieunternehmen vonstattengehen kann, zeigt das Beispiel der Heidelberger Druckmaschinen AG (Heidelberg) in Wiesloch/Walldorf. Dort hat man gemeinsam mit Linde Material Handling und dessen Vertragspartner Suffel Fördertechnik als Generalunternehmer ein komplett neues Logistikkonzept auf die Beine gestellt, das die Materialversorgung der Montagelinien von Offset-Druckmaschinen optimiert.
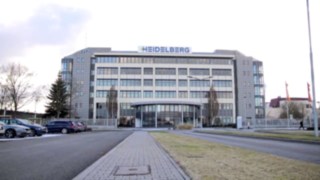
Die knallbunte Cornflakes-Packung auf dem Frühstückstisch, das schicke Hochglanz-Magazin in der Kaffeepause oder die edle Visitenkarte beim Business-Lunch: Obwohl sich unsere moderne Welt zunehmend digitalisiert, kommen wir nach wie vor überall mit Druckerzeugnissen oder bedruckten Waren in Berührung. Und so unterschiedlich diese auch sein mögen – die Wahrscheinlichkeit, dass sie auf einer Speedmaster von Heidelberg produziert wurden, ist denkbar hoch. Schließlich zählt das weltbekannte Unternehmen mit 11.500 Mitarbeitern zu den führenden Playern der Branche. Seinen Hauptsitz hat der Druck-Spezialist im baden-württembergischen Wiesloch/Walldorf – mitten in der wirtschaftsstarken Metropol-Region Rhein-Neckar, wo sich die vielbefahrenen Nord-Süd-Verkehrsachsen A5 und A6 kreuzen. Hier betreibt Heidelberg die größte und modernste Druckmaschinenfabrik der Welt; auf einem Quadratkilometer Fläche werden unter anderem die marktführenden Bogenoffset-Druckmaschinen in verschiedensten Formatklassen hergestellt.
Neue Herausforderungen –
neue Konzepte
Seit einigen Jahren beobachtet Heidelberg im Bereich der Kundenanforderungen einen stetigen Wandel hin zu mehr Individualität: „Früher haben wir am Standort überwiegend ähnliche Druckmaschinen gebaut“, erinnert sich der Leiter der Werklogistik Matthias Ehmler. „Heute fertigen wir sehr oft kundenspezifische Anlagen, wodurch die Variantenzahl stark gestiegen ist“, erzählt er.
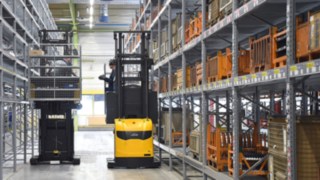
Schubmaststapler und Kommissionierer von Linde im Lager von Heidelberger Druckmaschinen
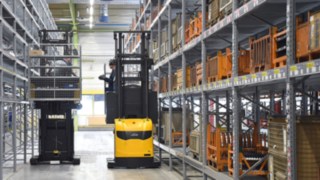
Schubmaststapler und Kommissionierer von Linde im Lager von Heidelberger Druckmaschinen
Dieser Customizing-Trend blieb an den Montagelinien nicht ohne Folgen: „Die Werker bewegten sich an den Montageplätzen immer öfter zwischen unübersichtlichen ‚Materialburgen‘. Je größer die Variantenzahl, desto mehr Teilebehälter standen dort herum. Das wirkte sich zunehmend negativ auf die Produktivität der Mitarbeiter aus“, schildert Ehmler die Situation. „Vor zwei Jahren haben wir deshalb ein Projekt zur Neuorganisation der Montage gestartet. Wir wollten die Produktionsflächen effizienter nutzen und das Material zum Werker bringen, nicht umgekehrt.“
Mit der angestoßenen Umstrukturierung der Montage hin zur Modulbauweise ging eine Neuorganisation der Intralogistik in der 600 Meter langen Halle einher. Materialien mit geringen Tagesbedarfen sollten künftig nicht mehr in Behältern vor Ort bereitgestellt, sondern auftragsbezogen auf Setwagen kommissioniert und mit Routenzügen an die Montagelinien gebracht werden. Dazu wurde am vorderen Ende der Montagehalle eine zentrale Kommissionier- und Konsolidierungsfläche mit Hochregal geschaffen. Vorgelagerte Pufferflächen wurden als Schnittstelle zu den internen Transportsystemen und als Übergabebahnhof für die kommissionierten Setwagen definiert.
„Unser Ziel war eine sichere, effiziente und flexible Materialversorgung bei bestmöglicher Flächennutzung“, beschreibt der Leiter der Heidelberger Werklogistik. Ein ambitioniertes Projekt, für dessen Umsetzung bei laufendem Betrieb verschiedenste Zahnräder perfekt ineinandergreifen mussten.
Kompetenter Partner gesucht
Mit einem umfangreichen Lastenheft gingen die Verantwortlichen in die Ausschreibungsphase. „Wir waren auf der Suche nach einem Partner, der den Regalbau und die Ausstattung mit Flurförderzeugen inklusive Flottenmanagement in Generalunternehmerschaft umsetzt. Gleichzeitig sollte natürlich der mit uns abgestimmte, fest kalkulierte Zeit- und Kostenplan eingehalten werden, damit wir uns ganz auf das Management der Grunddaten und Schulungen für die Mitarbeiter konzentrieren können“, umreißt Ehmler die Aufgabenstellung an die beteiligten Intralogistikunternehmen. Dass am Ende der Hersteller und Lösungsanbieter Linde Material Handling zusammen mit seinem Vertragspartner Suffel Fördertechnik den Zuschlag erhielt, hatte verschiedene Gründe: „Zum einen konnten die Linde-Geräte mit technischen Alleinstellungsmerkmalen punkten – beispielsweise bei den Bügelwagen-Anhängern des Routenzugs oder dem Hochhubkommissionierer. Zum anderen überzeugten uns Beratung und letztendlich natürlich auch die Vertragskonditionen,“ berichtet Ehmler.
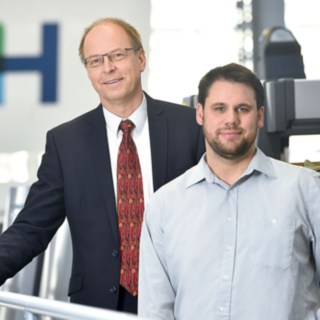
„Regalbau und Flurförderzeuge aus einer Hand in Auftrag zu geben, hat sich für uns in jeder Hinsicht bewährt.“
Matthias Ehmler, Leiter Werklogistik
Um die auftragsbezogene Bereitstellung der Teile an den Montagelinien zu ermöglichen, galt es zunächst, eine passende Lösung für das Kommissionierlager – und damit für das Herzstück des neuen Logistikkonzepts – zu finden: „Wir hatten bereits konkrete Ideen und Vorgaben im Lastenheft. Diese wurden nach Auftragserteilung sukzessive mit Linde und Suffel ausgearbeitet. Das Kommissionierlager sollte die Einlagerung von Groß- und Kleinteilen sowie ganzer Baugruppen zulassen, verschiedene Behältergeometrien erlauben und gleichzeitig den hohen Arbeitsschutz-Standards genügen“, fasst Projektleiter Stefan Heger die größten Herausforderungen zusammen.
Gut sortierter Supermarkt
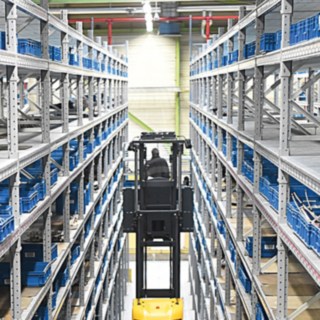
Das neue Hochregallager mit 13 Regalzeilen und 4.500 Sachartikelnummern fungiert als Supermarkt und besteht aus einem Breitgangbereich mit einer Gangbreite von 4,05 Metern und einem Schmalgang-Bereich mit drei Gassen. Im Breitgang übernehmen drei Schubmaststapler vom Typ Linde R14 das Einlagern des Materials, im Schmalgang übernehmen die insgesamt sieben Hochhubkommissionierer Linde V modular neben Kommissionieraufträgen auch die Nachschubversorgung. Bestückt wird das Lager aus drei unterschiedlichen Quellen: Großladungsträger gelangen über eine Brückenanbindung aus dem direkt angrenzenden, zentralen Versorgungslager zur Kommissionierfläche. Kleinladungsträger werden in einem separaten automatischen Kleinteilelager vorgepickt und über das interne Transportsystem angeliefert. Komplettierungen werden in der an die Kommissionierfläche angeschlossenen Vormontage bedarfsgerecht angefertigt.
Ergonomie und Sicherheit spielen wichtige Rolle
Kommissioniert wird im Hochregal ausschließlich mit den Hochhubkommissioniern Linde V modular. Vom Fahrzeug aus picken die Mitarbeiter das benötigte Material in bis zu 6,50 Metern Höhe und bestücken damit die circa 1,80 Meter hohen und 1,60
Meter breiten Drahtgeflecht-Setwagen, die maximal 500 Kilogramm Gewicht aufnehmen. Bis zu drei Kommissionieraufträge werden auf einem Setwagen platziert. Damit die Mitarbeiter leicht ins Regalfach greifen können, verfügen die Hochhubkommissionierer über integrierte Neigeschranken. „Diese Ausstattungsoption ist ein echtes Alleinstellungsmerkmal von Linde, das wir in unserem neuen Hochregal bestens brauchen können“, betont Jens Kernbach, Leiter Hallenlogistik bei Heidelberg. „Denn auch bei Heidelberg spüren wir den Demografiewandel und stehen unseren Mitarbeitern gegenüber in der Verantwortung.“
Damit das Kommissionieren im wahrsten Sinn des Wortes „reibungslos“ abläuft, fahren die Geräte innerhalb der Regalgänge induktionsgeführt. Auf diese Weise kann sich der Bediener voll und ganz auf den Pickvorgang konzentrieren und fährt im optimalen Abstand zum Regal. Zur weiteren Fahrzeugausstattung gehört ein Gangsicherheitsassistent, der das Gerät im Bedarfsfall kontrolliert bis auf Stillstand abbremst. „Beschädigungen am Regal oder an den
Geräten können wir nun ausschließen“, freut sich Projektleiter Heger. Zudem wurden die Lagereingänge mit Lichtschranken abgesichert. Sie lösen sofort einen Alarm aus, wenn Unbefugte das Areal betreten, das nur für Fahrzeuge freigegeben ist. Überdies ist die halbautomatische Lagernavigation von Linde bei den Geräten vorinstalliert und bietet Potential für weitere Optimierungen. Denn mit dieser RFID-gestützten Lösung navigieren die Hochhubkommissionierer im Regalgang ganz ohne Zutun des Bedieners in optimaler Kennlinie zum angewiesenen Stellplatz.
„Dank der induktiven Spurführung können wir Beschädigungen am Regal oder den Hochhubkommissionierern ausschließen.“
Stefan Heger, Projektleiter
Flexibel und platzsparend mit Routenzügen
Insgesamt drei Routenzüge - bei Linde Load Train genannt – bringen die bestückten Setwagen vom Übergabebahnhof zu den Werkern an die Produktionslinien. Sie setzen sich zusammen aus einem Schlepper vom Typ Linde P50 als Zugmaschine sowie einem bzw. zwei Bügelwagen mit Allrad-Lenkung und breiten Hublippen. Jeder Anhänger ermöglicht den gleichzeitigen Transport von je zwei Setwagen, die dank fehlender Mittelachse beidseitig aufgesetzt beziehungsweise entnommen werden können. „Das erlaubt es uns, die Wegstrecken flexibel zu planen“, sagt Projektleiter Stefan Heger. Ein weiterer Vorzug ist der geringe Platzbedarf des Linde Load Trains, der Spur treu auf einer Fahrbahn von 2,20 Meter Breite fährt.
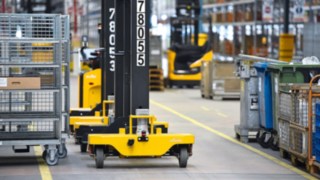
Positive Bilanz, aber Optimierung geht weiter
Auch nach Abschluss der Investition ist Werklogistikleiter Ehmler auf der Suche nach weiterem Optimierungspotenzial. Hilfe verspricht er sich unter anderem von dem Modul „Nutzungsanalyse“ der Linde-Flottenmanagementlösung. Ehmler: „Wir nutzen „connect:“ bereits seit vielen Jahren, um den Fahrzeugzugang zu kontrollieren und Schocks zu erfassen und haben damit sehr gute Erfahrungen gemacht. Jetzt können wir die Software auch nutzen, um unsere Prozesse zu optimieren und beispielsweise die Auslastung der Geräte noch weiter zu steigern.“
Mittlerweile ist es ein knappes Jahr her, dass die Neukonzeption der Intralogistik nach dem Prinzip Hochregallager, Hochhubkommissionierer und Routenzug bei Heidelberg umgesetzt wurde. Und das Fazit von Matthias Ehmler fällt denkbar positiv aus: „Wir haben das Projekt nicht nur im geplanten Zeit- und Kostenrahmen umgesetzt, sondern auch unser Ziel einer schlanken Logistik erreicht. Linde und Suffel haben sich damit eine positive Referenz bei uns geschaffen.“
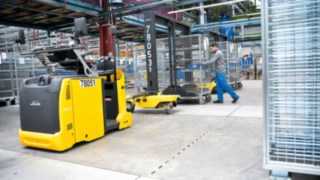